Service
One Stop Solution
HF-TI’s one-stop solution helps customers improve efficiency, reduce costs, consistent quality control, simplify their supply chain management and provide a better customer experience.
Convenience & Simplified Process
Customers only need to contact one supplier, saving time and process by meeting multiple needs from a single source.
Cost Savings & Efficiency Improvements
Provide more competitive prices and discounts, handle multiple demands more efficiently, and improve business operation efficiency
Consistency & Quality Control
Unify quality control standards to ensure that all products and services provided meet the same quality standards.
Single Responsible Party & Better Communication
Handle all related matters, including coordinating and integrating various products and services, helping to reduce communication errors and misunderstandings.
Service Process
HF-TI conducts a detailed analysis based on customer requirements, then proceeds with the design and manufacture of molds, and production after ensuring that the raw materials are well-prepared.
Upon completion of production, quality inspection is carried out, followed by surface treatment to enhance appearance and durability. Finally, the products are packaged and delivered to customers to ensure that high quality products meet customer expectations.
Needs Assessment
Customers provide 2D and 3D drawings for production requirement assessment.
Feedback
Provide design suggestions and production suggestions and provide complete DFM feedback
Graphic Design
After confirming the drawing with the customer, start making the mold drawing design
Preparation
After the graphic design is completed, start to prepare the mold.
Mold Making
Heat treatment, grinding, electrical discharge machining, wire cutting, CNC and other secondary processing and mold assembly
Trial Mold
Mold trial report, dimensional measurement, mold review and subsequent adjustments
Proofing and delivery
Sample recognition ensures product quality and compliance with specifications
Service Tracking
Understand customer needs and future production planning
Solve The Problem
Continuously improve products
Mass Production
Material production, additional processing, surface treatment
Quality Inspection
Incoming material inspection, in process inspection, final inspection
Ship
Ship according to packaging specifications
Quality inspection
HF-TI’s goal is to provide high-quality products. We record the production process through SOP, SIP, QC engineering sheets, etc., and undergo strict quality inspection to ensure that the products produced meet the highest standards and comply with ISO9001 and ISO14001 certifications.
IQC
IPQC
FQC
Check Sample Plate
HF-TI uses the problems discovered during each batch of production to produce inspection sample plates to ensure that the products produced meet standards and specifications, improve quality, reduce defects, and improve customer satisfaction.
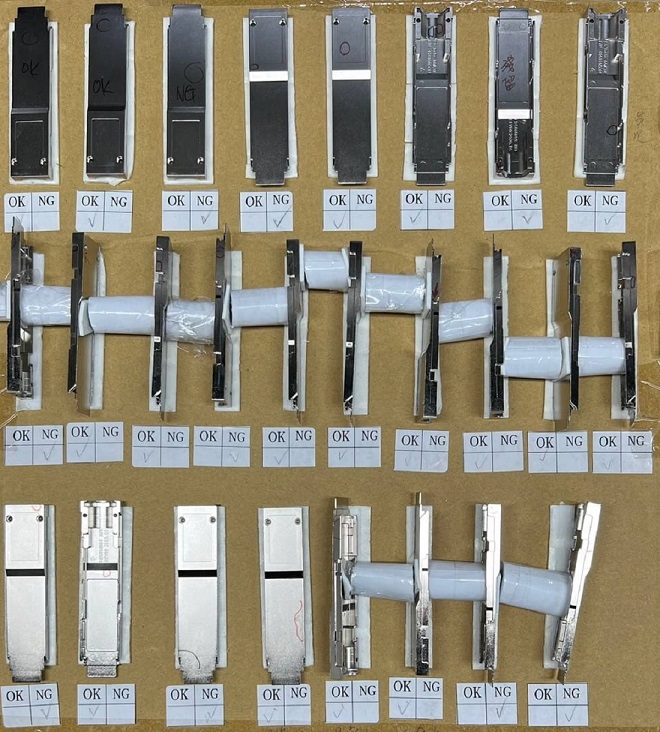
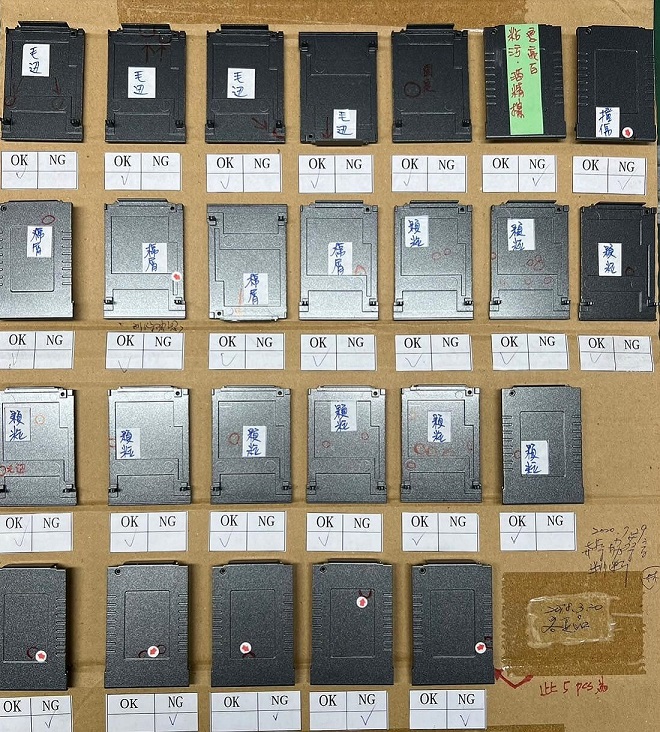
Certification
Our aim is to provide the best service and high quality products as well as one-stop service to all our customers. In order to achieve this goal, we are committed to the continuous improvement and control of total quality and have obtained ISO 9001 and ISO 14001 quality certification system.
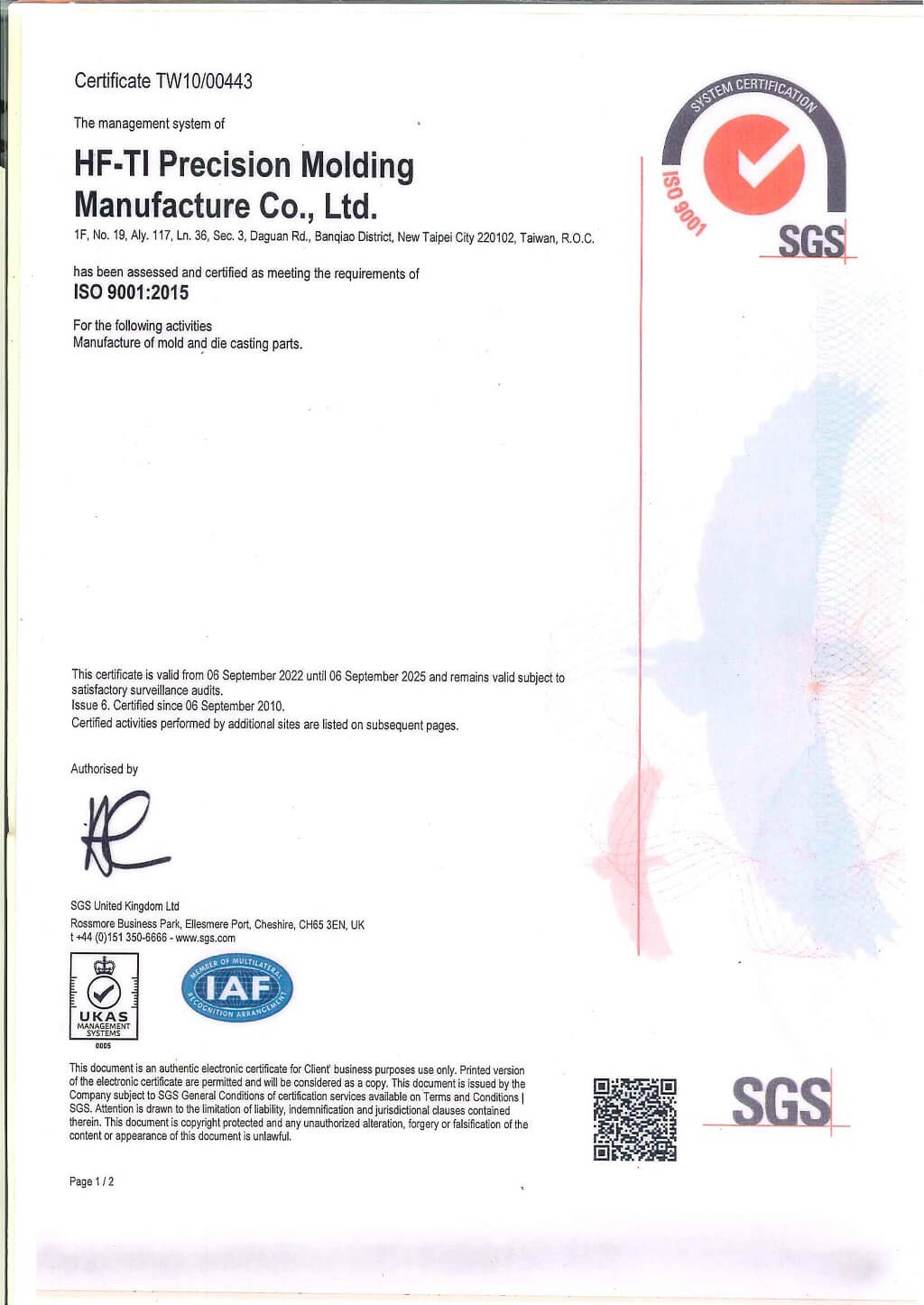
ISO 9001
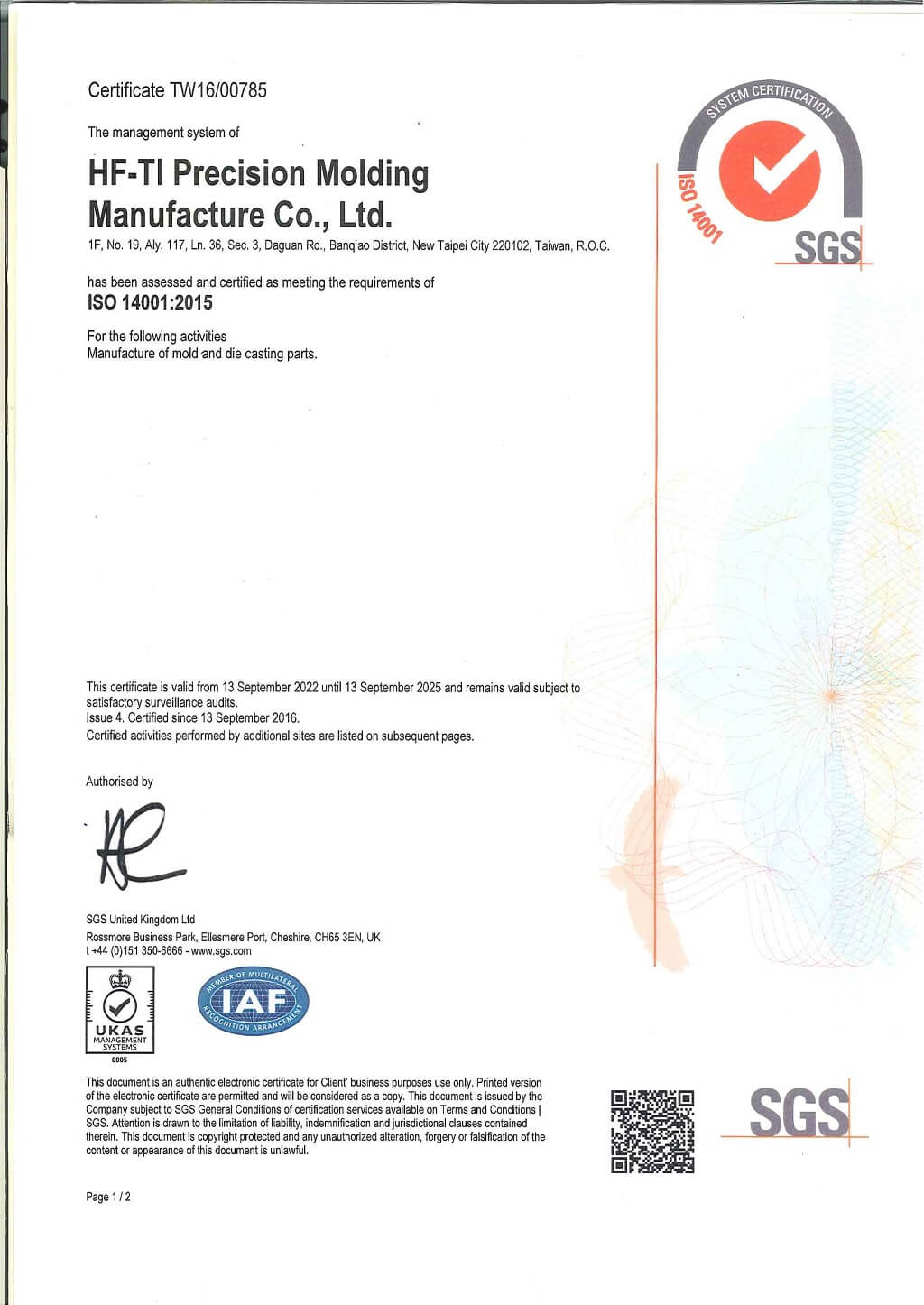